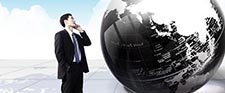
地址:長沙河西高新技術產(chǎn)業(yè)開發(fā)區(qū)觀沙嶺工業(yè)園
電話:0731-88619255
手機:13517481259
聯(lián)系人:李先生
傳真:0731-88619266
E-mail: csgtr@163.com
金屬表面漆前磷化處理工藝問題
作者: 湖南固特瑞 瀏覽量:4374 發(fā)布時間:2018-07-23
目前國內外研究和利用較多的是中、高溫磷化。但因其能耗大,處理工藝時間長,沉渣多而不利于現(xiàn)代化生產(chǎn)。為了提高磷化液的質量,降低能耗成本,磷化工藝已向低溫、少渣、優(yōu)質的方向發(fā)展,成為當前研究中的潮流 。本文主要研究了低溫鋅、錳系磷化,并確定了最佳配方和工藝條件。
1 實驗部分
1.1 試驗藥品
氧化鋅、碳酸錳、碳酸鈉、硝酸(65%)、磷酸(85cA、)、亞硝酸鈉、硝酸鎳、硫酸銅(均為分析純)。
1.2 磷化液的配制
將ZnO、MnCO3、NaCO3用水溶解調成糊狀.將H3PO4和HNO3,混合在一起.將上述兩部分液體慢慢混合,攪拌反應完全.反應完全后得無色透明溶液,因反應放熱,操作時要特別注意安全.待反應完全后加人硝酸鎳,攪拌至全部溶解.靜置熟化1 h以上,備用.若配制工作液需將上述磷化液稀釋20倍,加入適量促進劑,用NaCO3調整酸度至工藝范圍,攪拌均勻,化驗分析備用.
1.3 磷化膜性能測定
1.3.1 目測法外觀檢驗
采用目測法外觀檢驗是現(xiàn)場評價磷化膜質量的最簡單而有效的手段,一般檢驗項目有:晶體粒度、均勻性、色調、光澤、斑點、粉化情況等,可進行大體上的判斷.
1.3.2 微觀結構顯微鏡法
用電子顯微鏡將磷化膜放大100~1 000倍,觀察結晶形狀、尺寸大小及排布情況.結晶尺寸小些為好,一般控制在幾十微米以下,排布越均勻,孔隙率越小越好 .
1.3.3 腐蝕性能測定法
最常用的是硫酸銅點滴實驗法.在室溫(15~25 。C)下,在未浸油的磷化零件表面上滴一滴3%硫酸銅溶液,同時啟動秒表,30s后不出現(xiàn)玫瑰紅班為合格.
2 結果及討論
2.1 主要成分的作用與影響
2.1.1 磷酸二氫鋅
配制磷化液時碳酸錳用量為12 g/L,碳酸鈉用量為18 g/L,硝酸(65%)用量為135 g/L,磷酸(85%)用量為210g/L,亞硝酸鈉0.4 g/L,硝酸鎳18 g/L,反應溫度為40℃,磷化時間3 min,磷酸二氫鋅是主要的成膜物質,可由氧化鋅與磷酸反應制取.隨著磷酸二氫鋅用量的增加,磷化膜的耐腐蝕性提高;達到一定量時,磷化膜的耐腐蝕性隨磷酸二氫鈉用量的增加反而下降.這是因為磷酸二氫鋅主要起調節(jié)總酸度的作用,含量過高時,成膜速度快,膜層粗糙、疏松、附著力差,表面有浮灰;含量過低時,溶液成分變化快,調整困難,且磷化能力較弱,甚至膜薄不成膜,進而導致磷化膜的耐腐蝕性下降.通過實驗確定氧化鋅最佳用量為80一90g/L。
2.1.2 氧化促進劑
其他反應條件同2.1.1,氧化鋅為85 g/L,一般常溫低溫型磷化采用NO3-/NO2-、NO3-/ClO3-/NO2-;氧化促進劑體系較好,不僅成膜速度快,磷化膜形成結晶細密,促進劑主體NO2-;測定非常方便,所以槽液管理簡單,不易出現(xiàn)問題.對NO3-/ClO3-;有機硝基物促進劑體系,它雖不需要經(jīng)常補加,但由于主促進劑ClO2-;、有機硝基物的測定比較復雜,在實際應用中當出現(xiàn)促進劑過量或不足時槽液會變成深棕色,使總酸度、游離酸度的化驗帶來不便.本實驗促進劑主要成分為NO3-/NO2-體系.這種促進劑體系效果較好,成膜速度快,且結晶細致.但促進劑用量一定要控制在規(guī)定的范圍內,含量過低會使磷化膜表面不均,含量過高又會使Fe+2聚集過多,磷化膜易生黃色銹跡.通過實驗確定硝酸最佳用量為130~140 g/L。
2.1.3 磷化液中鎳離子和錳離子的影響
其他反應條件同2.1.1,氧化鋅為85 L,調整硝酸鎳和碳酸錳的用量,實驗結果如圖1~2。
鎳是比鋅電位高的二價金屬,能參與成膜,部分地置換出磷化膜中的鐵離子形成新的結晶活性中心,能促進成膜,細化晶粒,增強膜層結合力,降低了磷化溫度,縮短了磷化時間.鎳鹽的加入量太少無作用,加入最大,沒有不利影響,但會增加磷化液的成本;錳離子參與成膜,可提高磷化膜的硬度、耐腐蝕性和結合力,降低磷化處理溫度、提高反應速度、降低膜厚使磷化膜顏色加深,并帶有金屬光澤,還可降低昂貴的金屬鎳的用量.通過實驗確定硝酸鎳的用量為1O一20 g/L,碳酸錳的用量為l0一l5 g/L。
2.2 磷化工藝的影響
2.2.1 溫度的影響
其他反應條件同2.1.1,改變反應溫度,實驗結果見圖4。
溫度適當升高,雖然能激活能壘低的點也能成為結晶“活性中心”,使晶核數(shù)目增多,結晶速率加快.但溫度過高,F(xiàn)e+2大量產(chǎn)生,生成大量沉渣,造成成分不穩(wěn)定,消耗磷化液,使工件表面有掛灰現(xiàn)或不能生成膜層,易返黃,耐蝕性差,所以磷化時間隨溫度而定.將磷化溫度控制在35—45℃之間,既能保證適當?shù)牧谆俣群湍淤|量,還能減少沉渣產(chǎn)生,穩(wěn)定槽液穩(wěn)定性也差表2氧化鋅對磷化膜性能的影響,且磷化膜層粗大耐蝕性差,同時槽液的穩(wěn)定性也差;溫度低,磷化速度減慢,膜層不連續(xù)。
2.2.2 酸度的影響
磷化工藝中控制槽液的PH值比控制酸度比更合適。因為無論磷化液是由H3PO4或磷酸鹽配制, 它們在水溶液中都同時存在著多步離解平衡:
因為磷化體系中/=K2(25℃,K2=0.013), 將(2)、(3)式代入到平衡常數(shù)K2的表達式中整理得到:
C總=5.7×10-5( +7.6 ×10-2 +4.8×10-10 +2.1×10-22 (4)
在滿足K2表達式的前提下,磷化液的PH值與配成磷化液的H3PO4或磷酸鹽的總濃度之關系可由(4)式計算出來,計算結果見表4。
2.2.3 磷化時間的影響
其他反應條件同2.1.1,改變反應時間, 磷化時間是一個重要的影響因素,磷化時間短,能節(jié)約成本,但工藝不穩(wěn)定,不易控制,磷化膜性能不穩(wěn)定;磷化時間長,成本高,獲得的磷化膜質量差,結晶面上再結晶,膜層粗糙較厚,附著力差.本工藝磷化時間應控制在3 min左右,能形成理想的磷化膜.
3 結論
通過對鐵板板材進行大量的重復試驗,得出了最優(yōu)的工藝配方:氧化鋅用量為80—9O g/L,碳酸錳l0~l5 g/L,碳酸鈉15—20 g/L,硝酸(65%)130—140 g/L,磷酸(85%)200—220 L,亞硝酸鈉0.2—0.5 g/L,硝酸鎳l0~20 g/L.本工藝屬于低溫鋅系磷化,使用了多種金屬的酸式鹽作為成膜物質,控制溫度在35—45。c,總酸/游離酸在18—25之間,磷化時間3—5 min,比普通鋅系磷化工藝得到的磷化膜耐腐蝕性好,磷化溫度低,時間短,磷化膜耐蝕性好,與涂層附著力好,耐沖擊性好,均勻性好,改善了普通鋅系磷化工藝沉渣多,能耗大,磷化液不耐用等缺點。
上一篇:
長沙固特瑞應用中溫磷化技術的幾點體會
下一篇:
磷化技術的發(fā)展概況